A Case Study: Predictive Maintenance with AI in Manufacturing
Analyze how a manufacturing company adopted AI tools to predict machinery breakdowns. Highlight the tools used, the challenges faced during integration, and how these solutions minimized downtime and increased production reliability.
CASE STUDY
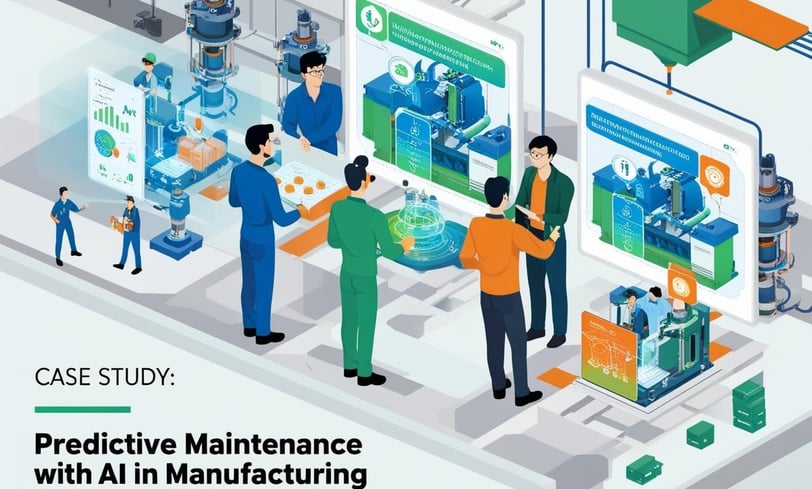
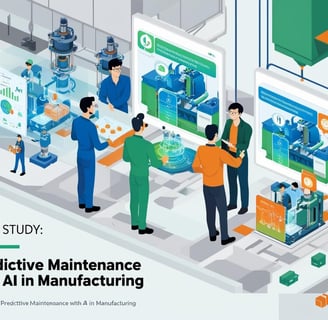
In the rapidly evolving landscape of manufacturing, efficiency, reliability, and cost-effectiveness are paramount. Traditional maintenance methods often involve either reactive responses to equipment failure or scheduled preventive maintenance, both of which can be costly and disruptive. Enter predictive maintenance powered by artificial intelligence (AI) — a transformative approach enabling manufacturers to foresee and mitigate equipment failures before they occur.
This blog post delves into the mechanics, benefits, and challenges of predictive maintenance in manufacturing, presenting a detailed case study to illustrate its potential. Discover how AI tools are reshaping maintenance strategies and setting new standards in operational excellence.
What Is Predictive Maintenance?
Predictive maintenance involves the use of advanced analytics, AI, and Internet of Things (IoT) technologies to monitor equipment performance and predict when maintenance is required. Unlike reactive or preventive maintenance, predictive maintenance focuses on anticipating failures based on real-time data, minimizing downtime and extending the lifespan of machinery.
Key Components of Predictive Maintenance
1. IoT Sensors: Collect real-time data such as temperature, vibration, and pressure from equipment.
2. AI Algorithms: Analyze historical and real-time data to identify patterns and predict failures.
3. Machine Learning Models: Continuously improve prediction accuracy by learning from new data.
4. Cloud Platforms: Provide centralized storage and processing for vast amounts of data.
5. Dashboards and Alerts: Offer intuitive interfaces for maintenance teams to monitor equipment and receive actionable insights.
Benefits of AI-Driven Predictive Maintenance
1. Reduced Downtime
Predictive maintenance minimizes unexpected equipment failures, ensuring uninterrupted production.
2. Cost Savings
By addressing issues before they escalate, manufacturers save on repair costs and avoid production losses.
3. Prolonged Equipment Lifespan
Timely maintenance reduces wear and tear, extending the operational life of machinery.
4. Enhanced Safety
Identifying potential hazards early ensures a safer working environment for employees.
5. Data-Driven Decision Making
With AI-driven insights, maintenance teams can make informed decisions, optimizing resource allocation and scheduling.
Challenges in Implementing Predictive Maintenance
Despite its advantages, predictive maintenance poses several challenges:
1. High Initial Investment: Deploying IoT sensors, AI models, and data infrastructure requires significant capital.
2. Data Quality and Integration: Inconsistent or incomplete data can hinder prediction accuracy.
3. Skill Gap: Maintenance teams may require upskilling to interpret AI-driven insights.
4. Scalability: Adapting predictive maintenance systems to large-scale operations can be complex.
5. Cybersecurity Risks: IoT-connected devices are susceptible to hacking, necessitating robust security measures.
Case Study: Predictive Maintenance at XYZ Manufacturing
Background
XYZ Manufacturing, a mid-sized producer of automotive components, struggled with frequent machine breakdowns that disrupted production schedules and inflated maintenance costs. The company decided to implement an AI-driven predictive maintenance system to enhance operational efficiency.
Implementation
1. Objectives:
- Reduce unplanned downtime by 50%.
- Lower maintenance costs by 30%.
- Increase overall equipment effectiveness (OEE).
2. Technology Stack:
- IoT Sensors: Installed on critical machinery to capture real-time data.
- AI Platform: Used machine learning algorithms to analyze sensor data and predict equipment failures.
- Cloud Storage: Enabled centralized data processing and analytics.
- Mobile Alerts: Delivered real-time updates to maintenance teams.
3. Process:
- Data Collection: IoT sensors gathered data on temperature, vibration, and operational cycles.
- Model Training: Historical maintenance records and sensor data were used to train AI models.
- Monitoring and Alerts: The system continuously monitored equipment performance, sending alerts when anomalies were detected.
Results
After one year of implementation, XYZ Manufacturing reported:
1. Downtime Reduction: Unplanned downtime decreased by 55%, exceeding initial expectations.
2. Cost Savings: Maintenance costs were reduced by 35%, translating to significant financial gains.
3. Productivity Boost: Overall equipment effectiveness improved by 20%.
4. Improved Safety: Early detection of potential issues minimized safety risks, earning the company industry accolades.
Employee Feedback
Maintenance staff lauded the system for its user-friendly interface and accurate predictions, though they emphasized the importance of training to fully utilize the AI-driven insights.
Future Trends in Predictive Maintenance with AI
1. Edge Computing
Processing data closer to the source (on the factory floor) will reduce latency and enhance real-time analytics.
2. AI-Powered Prescriptive Maintenance
Beyond predicting failures, AI will offer actionable recommendations, such as specific repair actions or parts replacement.
3. Advanced IoT Integration
Emerging IoT devices with higher sensitivity and broader metrics will further improve prediction accuracy.
4. Digital Twins
Virtual replicas of physical assets will simulate different scenarios, enabling proactive maintenance strategies.
5. Blockchain for Data Security
Blockchain technology will ensure secure and transparent data sharing among stakeholders, addressing cybersecurity concerns.
Conclusion
Predictive maintenance powered by AI represents a paradigm shift in manufacturing, blending advanced analytics with practical applications to revolutionize equipment management. The case of XYZ Manufacturing highlights how adopting this technology can lead to tangible benefits, including reduced downtime, cost savings, and improved safety.
However, the path to successful implementation requires addressing challenges like data integration, cybersecurity, and skill gaps. As AI tools continue to evolve, their potential to redefine maintenance practices in manufacturing is boundless.
For manufacturers aiming to stay competitive in the digital age, embracing predictive maintenance is not just an option—it’s a necessity. Dive deeper into AI-driven solutions at "How AI Saved $1 Million Annually for a Manufacturing Company" , your go-to resource for the latest in AI innovation and tools.
Read more relevant articles at: "AI in Logistics: Optimizing Supply Chains for Global Enterprises".
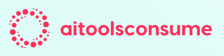
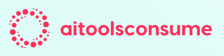